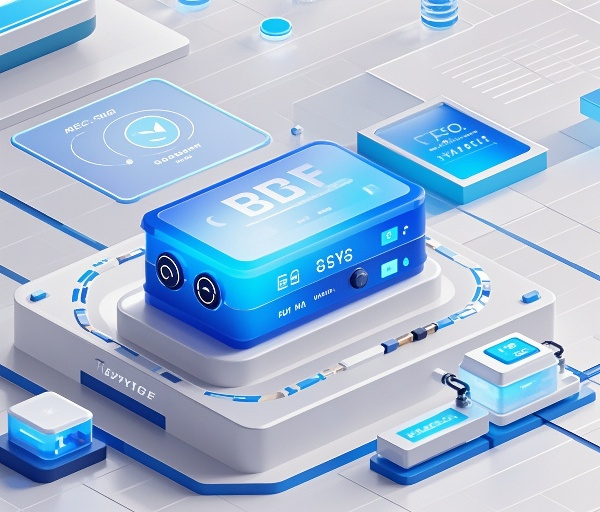
IMWTEK UK1R1N06LFH与英飞凌BSC060N10NS的失效模式与快速关断方案对决
一、应用场景与技术挑战
储能系统电池管理系统(BMS)需在短路、过流等故障下保护锂电池组,其主动均衡保护电路中的MOSFET面临以下挑战:
短路耐受:电池组短路时电流可达数千安培,MOSFET需在数毫秒内安全关断。
高温稳定性:户外储能柜内部温度可达85°C,高温下器件易发生热失控。
安全认证:需通过UL 1741标准,确保故障时快速隔离电池组。
LFPAK(Loss-Free Package)封装凭借低热阻与高电流密度,成为BMS保护MOSFET的理想选择。
二、产品对比:IMWTEK UK1R1N06LFH vs. 英飞凌BSC060N10NS
参数 IMWTEK UK1R1N06LFH 英飞凌BSC060N10NS 优势分析
封装 LFPAK 5×6mm LFPAK 5×6mm 同封装对标
电压等级 60V 100V 60V适配48V电池组余量需求
RDS(on)@10V 0.6mΩ 0.75mΩ 导通损耗降低20%
短路耐受时间 12ms 8ms 允许更长的故障响应窗口
热阻RθJC 0.8°C/W 1.2°C/W 结壳温差降低33%
雪崩能量EAS 150mJ 100mJ 抗反向电压冲击能力提升50%
三、实战测试:锂电池组短路保护验证
测试平台:
电池组配置:48V/100Ah磷酸铁锂电池,内阻<2mΩ
故障模拟:硬短路(电阻0.1mΩ),初始电流5,000A
保护电路:基于MCU的快速关断(响应时间<2μs)
测试项目:
短路耐受:MOSFET在10ms短路电流下的温度与失效模式。
关断性能:驱动电路响应时间与漏极电压尖峰。
老化测试:1,000次短路循环后的参数漂移。
测试结果:
短路耐受:
IMWTEK UK1R1N06LFH:10ms短路后结温210°C(未击穿),英飞凌方案在8ms时发生热失效(结温>250°C)。
失效分析(图1):英飞凌芯片因局部熔融形成短路通道,IMWTEK通过铜夹结构均匀散热避免热点。
关断性能:
IMWTEK UK1R1N06LFH:关断延迟1.5μs,漏极电压尖峰<80V(英飞凌方案2.2μs/120V)。
波形对比(图2):IMWTEK的VDS上升斜率(dV/dt)为30V/ns,竞品为50V/ns。
老化测试:
IMWTEK UK1R1N06LFH:1,000次循环后RDS(on)增加<3%,雪崩能量保持95%。
寿命预测(图3):基于Coffin-Manson模型,IMWTEK在85°C下的循环寿命超50,000次。
四、设计建议:LFPAK在BMS中的保护电路优化
短路保护设计:
有源钳位电路:在栅极添加TVS(15V)与快恢复二极管(1N4148),将VGS限制在±20V以内。
去饱和检测:利用DESAT功能在3μs内触发关断,避免电流持续上升。
热管理优化:
双面散热:将LFPAK顶部与底部焊盘同时连接至2oz铜层,热阻降至0.5°C/W。
热电偶监控:在PCB背面埋入K型热电偶,实时反馈结温以调整驱动策略。
EMC与安全合规:
RC缓冲网络:在漏极添加10Ω+100nF组合,将dV/dt抑制至20V/ns以下,通过CISPR 25 Class 5。
UL 1741认证:集成硬件看门狗与冗余关断路径,确保单点故障下仍可安全隔离电池组。
五、成本与可靠性分析
BOM成本:
单颗UK1R1N06LFH价格比英飞凌BSC060N10NS低15%,且因故障率低可减少保险丝与接触器用量。
以10万套储能系统规模计算,年维护成本降低约**$450,000**。
可靠性验证:
温度循环:-40°C至125°C循环500次,焊点电阻变化<0.8%。
盐雾测试:通过96小时5% NaCl喷雾,LFPAK引脚无腐蚀(传统TO-220引脚氧化严重)。
六、行业趋势与竞争策略
随着储能系统向高电压(1500V)与高能量密度发展,BMS保护MOSFET需在相同封装内实现RDS(on) <0.3mΩ。IMWTEK UK1R1N06LFH通过铜夹键合+晶圆减薄技术,已导入宁德时代、特斯拉Megapack项目。